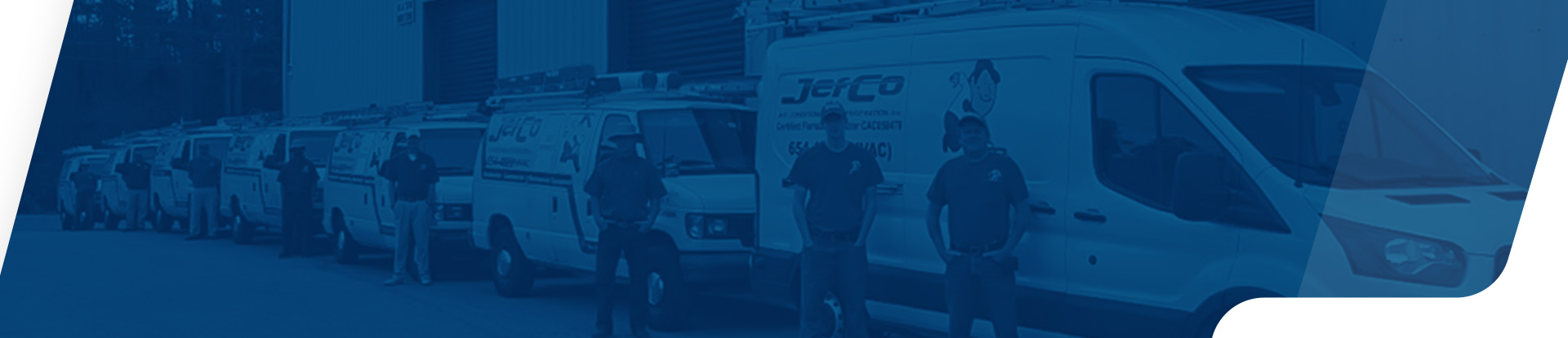
Ice Machine Services in Santa Rosa Beach
Reliable access to ice is crucial for many Santa Rosa Beach businesses. At JefCo Air Conditioning & Refrigeration, we understand this necessity. Our dedicated team is ready to offer the service you need to keep your ice machines operating effectively, and it’s a disruption to your daily operations.
We are committed to providing comprehensive support for your ice machine needs, including regular upkeep, necessary repairs, and the installation of new units. Recognizing the impact of downtime, we prioritize a prompt response to ensure your ice supply remains consistent.
JefCo Air Conditioning & Refrigeration is focused on your satisfaction and stands by the quality of our service. We offer transparent service options and are committed to meeting your specific requirements.
Call (850) 616-2183 to schedule a free estimate for ice machine services
in Santa Rosa Beach today.
The Benefits of Regular Ice Machine Maintenance
Taking care of your ice machine isn’t just good practice—it’s a smart way to keep your business running smoothly. Regular maintenance can prevent unexpected breakdowns, save you from costly emergency repairs, and extend the lifespan of your equipment. By addressing wear and tear early, you reduce the chances of larger, more expensive issues down the line.
Clean and well-maintained ice machines also produce better-quality ice, which is critical for upholding hygiene standards and keeping your customers happy. Nothing undermines customer confidence like cloudy or poorly made ice, so staying on top of the upkeep ensures you deliver the best possible experience.
Proactive maintenance saves you money—it minimizes disruption. Spotting potential issues early allows timely repairs that don’t interfere with your operations. Ultimately, prioritizing regular service isn’t just about fixing problems; it’s an investment in reliability, performance, and peace of mind.
Identifying Common Ice Machine Problems
Recognizing issues with your ice machine early can prevent larger complications down the line. One common problem is reduced ice production, which could be caused by a clogged water filter or improper temperature settings. Regularly inspecting the machine for debris buildup or blockages in the water line can help address this quickly. Additionally, strange noises during operation may indicate that worn-out components, such as the compressor or fan, require immediate attention to avoid further damage.
Another frequent concern is ice that appears cloudy or misshapen, often due to poor water quality or scaling on internal surfaces. Hard water deposits can accumulate over time, affecting both the functionality and hygiene of the machine. Cleaning the evaporator plate and maintaining the proper balance of water treatment can restore ice quality.
Leaks are also a red flag many operators encounter. These may result from cracked hoses, loose connections, or drainage issues. Routinely checking for visible leaks and ensuring proper drainage flow can prevent unnecessary downtime. Addressing these common challenges promptly helps maintain efficient operations and uninterrupted service for your customers.
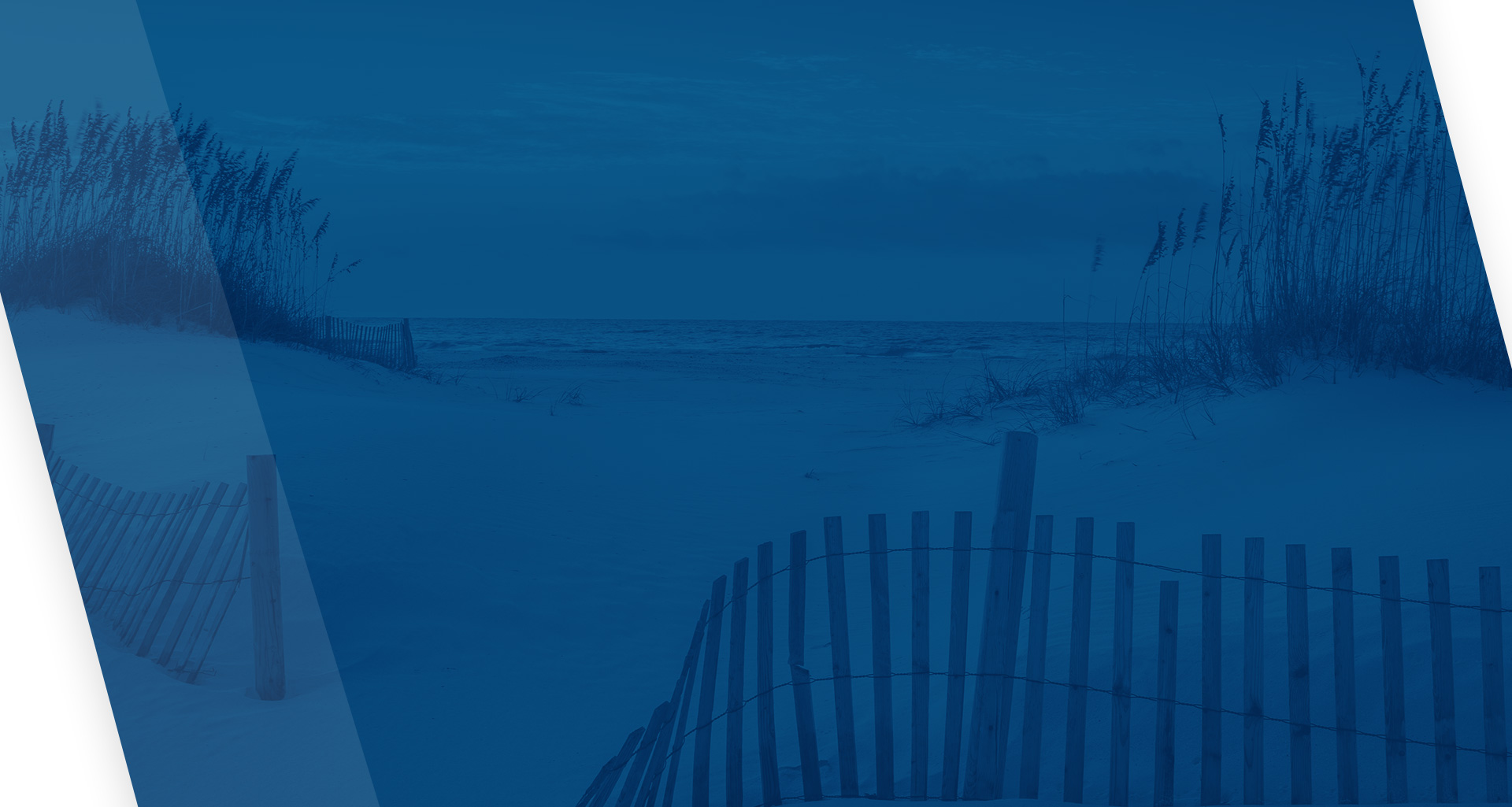
Hear From Our Happy Customers
At JefCo Air Conditioning & Refrigeration, your satisfaction is our priority! See for yourself what our customers have to say about working with us.
-
“Purchased a new air conditioning system from JefCo. Incredible local company. Knowledgeable, professional, skilled, prompt, polite. A joy to be served by them!”- Cyndy P.
-
“Daniel was courteous, polite and took the time to explain the issue and discussed the part replacement before repairing and completed the job in an hour. Very efficient and professional!”- Wes G.
-
“On time professionals, quick, efficient, great service, cleaned up everything, nice and friendly! Love the new AC and thermostat! Thank you for a job well done!”- Frankie W.
-
“They serviced my Frozen Yogurt machine. The tech was very friendly and did a great job chasing down the refrigerant leak. He paid very close attention to detail when repairing. Thank you! I will be using your company again for future repairs.”- Jason F.
-
“He is so patient, always explains everything to Larry & answers all of our questions. He is very knowledgeable of the equipment. We are pleased with John, Jefco Air, & all of their friendly, helpful employees. Top notch!!”- Vanessa F.
-
“Dylan has been out to do the yearly service on our multiple AC units for the last few years and does a fantastic job every time! He is on time, courteous, knowledgeable, & professional!”- Melissa E.
-
“Always get great service from everyone at Jefco! They are available. Quick to respond. Great at communicating. I highly recommend them!”- Jason A.
-
“I don't think I can say enough good things about JefCo Air Conditioning & Refrigeration. They were super friendly, super professional, and an all-around great company. I am beyond thankful.”- Denise G.
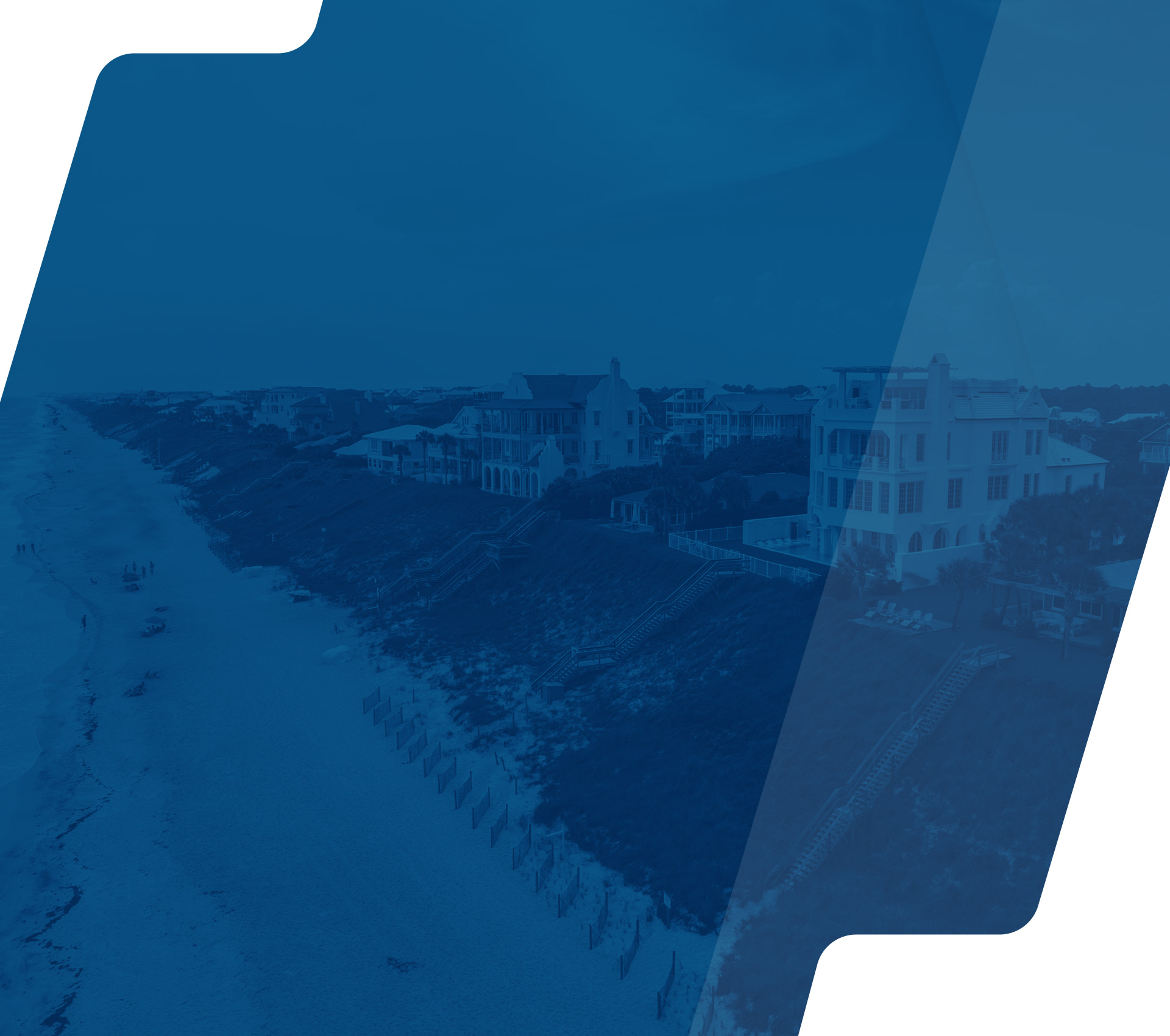